Precision Metal Parts Manufacturing
Petersen Precision is the turnkey manufacturing partner you need for your challenging projects. Our extensive array of manufacturing technologies and expertise will bring your product to market on time with support from prototype to volume production.
Our ISO 9001/AS9100 certified organization operates process technologies including Fine Blank Stamping, Double Disc Grinding, Fine Grinding, Lapping, Creep Feed Form Grinding, Centerless Grinding, Surface Grinding, as well the full complement of CNC machining capability with production 4-axis Horizontal Mills, Vertical Mills, CNC Swiss Screw machines, CNC Lathes, Wire EDM and more all under one roof. These processes are ideal for your products that require more complex, intricate designs and those that require tight tolerances.
Why Choose Petersen Precision?
Petersen Precision is a high-volume manufacturer of precision metal parts. When you choose Petersen for your regular metal parts orders, you experience quick turnaround and product development as our technologies are all in-house.
Our customers also appreciate a high level of service as we work with you to manufacture and engineer the metal products your application requires. Our team is innovative while also having 55 years of experience in metal fabrication capabilities. You can count on reasonable prices, great communication, and fast product development.
Partner with us for your precision metal fabrication needs. Contact us today about our supply agreement and partnership options.
Metal Fabrication Capabilities
We are experts in the manufacturing of precision metal parts through a variety of processes. With in-house tool design and fabrication, we can support your time-to-market and product cost needs. These precision technologies include:
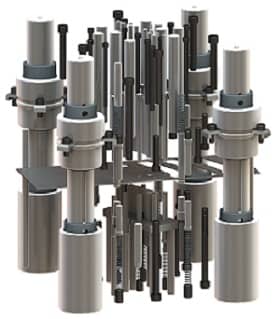
Fine Blanking
This specialized metal part stamping process can produce accurate, intricate parts to very tight tolerances, with clean-sheared edges and detailed coined features. Our extensive inventory of fine blank presses ranging from 40 to 250 tons is ready to meet your production needs.
CNC Machining
Petersen Precision maintains a large inventory of late-model high-end CNC machining centers configured with pallet changing capability to guarantee high utilization, flexibility, and 24-hour production. Our experienced team programs with MasterCam software, and our state-of-the-art tool setting capability and real-time inspection sampling ensure excellent part quality and repeatability on the most challenging materials.
Precision Grinding
Petersen Precision has a wide variety of grinding technologies available to produce parts with challenging design needs for precision and geometry. Our grinding processes include Creep Feed form grinding, Double Disc Grinding, Blanchard rotary surface grinding, CNC surface grinding, Centerless Grinding, OD Grinding and Honing. These processes give us the capability to produce complex parts with very tight tolerances.
High Production Lapping & Fine Grinding
We specialize in lapping processes that achieve the finest level of flatness and thickness precision. Loose abrasive polishing (also known as lapping) flattens and polishes metal surfaces to produce a fine finish. Using this process, we can produce precision metal parts with extremely flat surfaces. We also have the technology for cylindrical lapping of round surfaces to tolerances in the millionths.
Our parallel fine grinding capability compliments ground or machined parts with precision quality not achievable by other means. The fine finish and tight tolerance capability for flatness, parallelism, and thickness in this high-production process is a cost-effective way to produce precision flat parts.
Wire EDM Machining
Wire EDM is an accurate machining process that can produce high-precision parts using any metal. Petersen has a large inventory of late-model Mitsubishi wire EDM machines ready to support front-end part prototypes, volume part production, and all internal tooling needs. We have an additional 4th-axis rotary EDM capability for producing complex geometries, and this technology can manage wire sizes down to .004” diameter for fine features and small radius capabilities.
Deburring, Finishing & Cleaning High-Volume Parts
Machining, grinding, and fine blanking precision parts require an equally wide variety of deburring, finishing, and cleaning processes to meet end part specifications. Petersen maintains such processes including vibratory deburring, rotary barrel deburring, centrifugal disc deburring, and continuous sand & brush deburring. Our operators are skilled and experienced when an application requires hand deburring.
Our cleaning technologies include the automated Eco-Clean self-contained alcohol vapor degreasing system and Crest aqueous ultrasonic DI water cleaning systems. These cleaning technologies produce near-cleanroom part cleanliness, leaving them ready for plating or other surface treatment.
Value Add Processing Services
In addition to the various manufacturing technologies above, Petersen performs light component assembly work, bend forming, micro-abrasive blasting, and laser marking. Our engineering team can design and build customized solutions for assembly, pin insertions, and testing for your parts or assemblies that provide cost-effective and repeatable automated solutions that solve your team’s problems.
Precision Machining Industries Served
We serve high-end OEMs and specialty industries from the first prototype to high-volume production under one company umbrella of facilities. Our engineers will help your team develop cost-effective solutions to meet your most challenging precision part needs. We utilize statistical methods for quality control and engineering and our engineering team can support your PPAP validations to meet your Medical or Aerospace process approval requirements.
At Petersen Precision, we maintain a selection of qualified special process subcontractors to perform plating, passivation, and various types of heat treating that meet all industry standards, and many of the major OEM-approved supplier approvals. We have extensive knowledge of these processes and can help support your material and special processing needs.
Precision Metal Manufacturing for Specialty Industries:
- Precision Medical Devices
- Aerospace & Defense Machining
- Electronics & Semi-Conductors
- Tool & Hardware Components
- Scientific Instruments
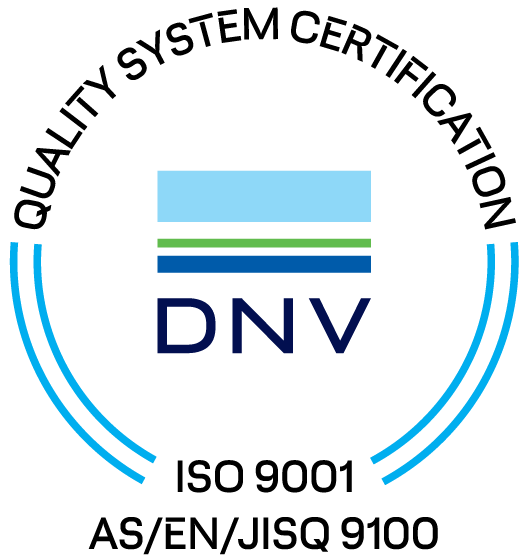
Dedicated to Delivering Top Quality Parts
At Petersen Precision, our quality management system is ISO9001 and AS9100 certified as well as ISO13485 compliant. We utilize our engineering expertise in concert with our quality system to develop statistically capable processes, document it so that it can be repeated, adjust it to meet the needs of our customers, and review it on a timely basis to ensure continuous improvement. We are experienced in capability studies and PPAP processes that support AS9100 and ISO 13485 product qualifications.
Petersen Precision will provide our customers with the highest quality products and services. Our goal is to achieve total customer satisfaction by meeting or exceeding customers’ requirements. We are committed to continuous improvement in every aspect of our business and throughout all levels of our organization.